The Benefits of Responsive Warehousing
In today's fast-paced, on-demand marketplace, the ability to move product quickly and efficiently is no longer a competitive advantage — it's a basic expectation.
For fast-moving businesses, whether in retail, e-commerce, manufacturing, or distribution, warehousing isn't just about storing goods. It's about having a partner who can scale, adapt, and respond as rapidly as your market does.
That's where responsive warehousing makes all the difference.
At Gustine Logistics, responsive warehousing isn't just a buzzword — it's the core of our operation. With over 80,000 square feet of scalable space, real-time inventory systems, and fast inbound and outbound operations, we provide the flexibility and speed that modern businesses demand.
So, what is responsive warehousing, and how can it improve your business operations?
What Is Responsive Warehousing?
Responsive warehousing refers to storage and logistics operations that can adapt quickly to changing inventory volumes, fulfillment timelines, and customer needs.
It means having the infrastructure, technology, and team to adjust with minimal disruption, whether you're scaling up for peak season or downsizing after a campaign.
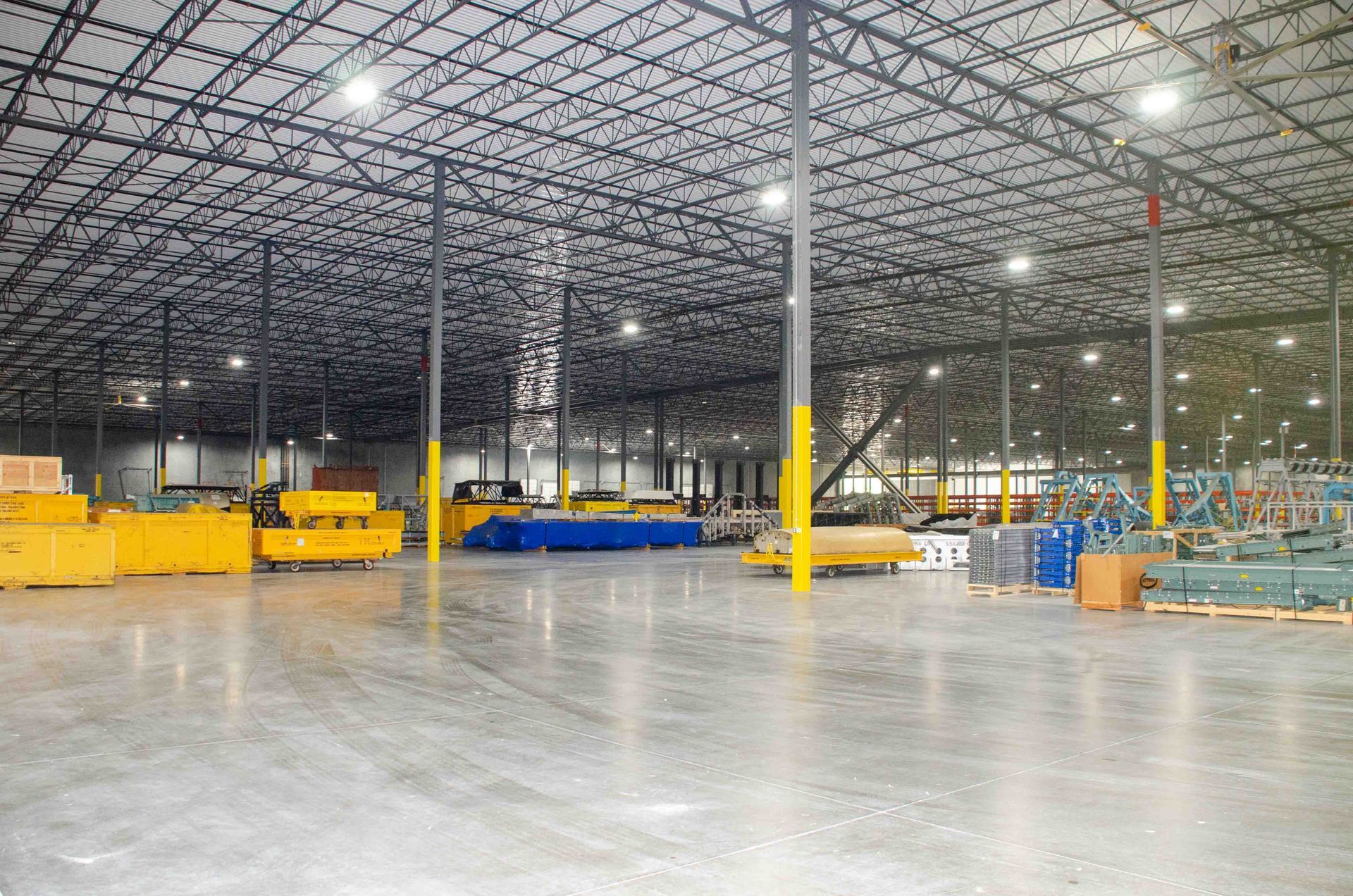
Why Fast-Moving Businesses Need Responsive Warehousing
Whether you're a growing e-commerce brand, a wholesale distributor, or a manufacturer working on just-in-time delivery, your success hinges on how fast and accurately you can get product to your customers.
Scalability on Demand
Fast-moving businesses often deal with unpredictable spikes in demand — product launches, seasonal sales, or promotional events. Traditional warehousing solutions often require long-term leases and fixed space, which can leave you either overpaying for unused capacity or scrambling for last-minute storage.
Gustine Logistics offers scalable space, meaning you only pay for what you need when you need it. Whether it's 1,000 or 80,000 square feet, we adjust with you quickly and seamlessly.
Faster Turnaround and Fulfillment
In today's environment, customers expect next-day or even same-day shipping. That puts enormous pressure on fulfillment operations. A responsive warehouse can quickly process inbound deliveries, prep items for dispatch, and get them back out the door without delay.
Our dock-to-stock and cross-docking services are designed to keep your inventory moving. With well-trained teams and efficient layouts, we reduce downtime and ensure fast throughput from receiving to shipping.
Real-Time Inventory Visibility
Responsiveness starts with accurate, real-time information. Without visibility into what's in stock, where it's located, or how it's moving, businesses can't make smart, timely decisions.
Gustine's integrated inventory management system gives you full, on-demand visibility. You'll know what's on hand, what's inbound, and what's been shipped — all in real time. This transparency reduces stockouts, prevents overstocking, and helps you respond proactively to changes in demand.
Cost Efficiency Without Long-Term Commitments
Long-term warehousing contracts can be a barrier for fast-moving or rapidly growing companies. They force you to predict future needs you may not fully understand, locking you into space or services that may no longer fit a few months down the road.
Our responsive model eliminates long-term commitment requirements, giving you the freedom to scale operations up or down based on real-time business needs. That means you can grow without the risk of being tied to inflexible costs.
Improved Customer Satisfaction
Ultimately, responsive warehousing supports your end customer. When you can fulfill orders faster, reduce errors, and react to market changes without disruption, your customers notice. On-time delivery and inventory availability are no longer optional — they're critical to retaining trust and loyalty.
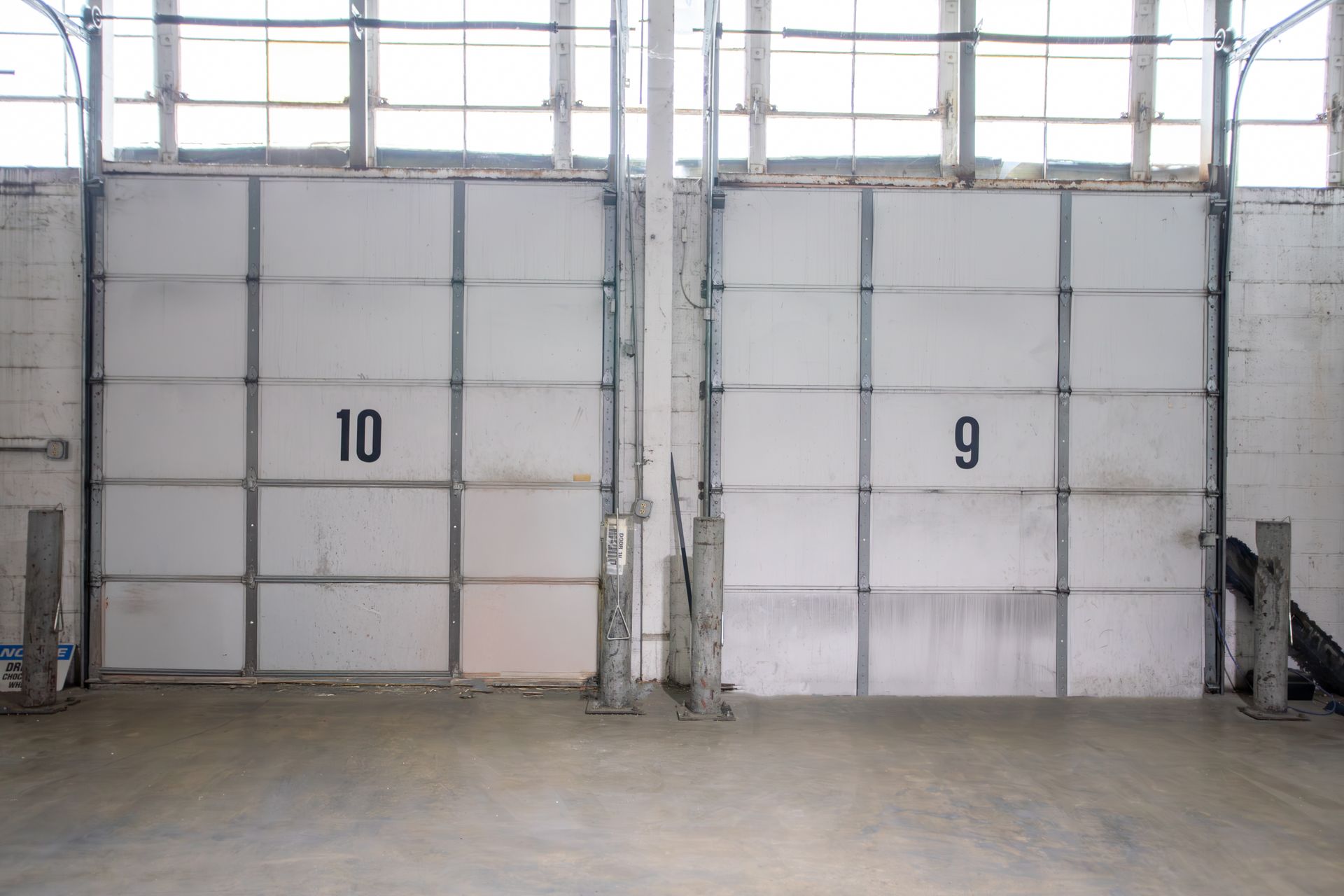
Example: Growing E-commerce Retailer
Suppose a mid-sized e-commerce company came to a responsive warehouse with a challenge: their current warehouse provider couldn't scale during seasonal surges, resulting in backorders and missed delivery deadlines.
By switching to our
flexible, responsive warehousing model, they would improve their operations across the board.
- Expand their storage footprint during peak holiday months
- Cut order fulfillment times
- Access real-time inventory tracking for more thoughtful planning
The result? Increased sales, fewer customer complaints, and a logistics setup that finally matched their growth ambitions.
Work With Gustine Logistics
Fast-moving businesses need more than just square footage — they need a logistics partner that understands the pace and pressure of modern commerce.
At Gustine Logistics, we've built our services around your reality: fluctuating demand, tight timelines, and the need for flexibility at every turn.
Looking for a warehouse that grows with you?
Contact Gustine Logistics today and discover how responsive warehousing can give your business a strategic edge.
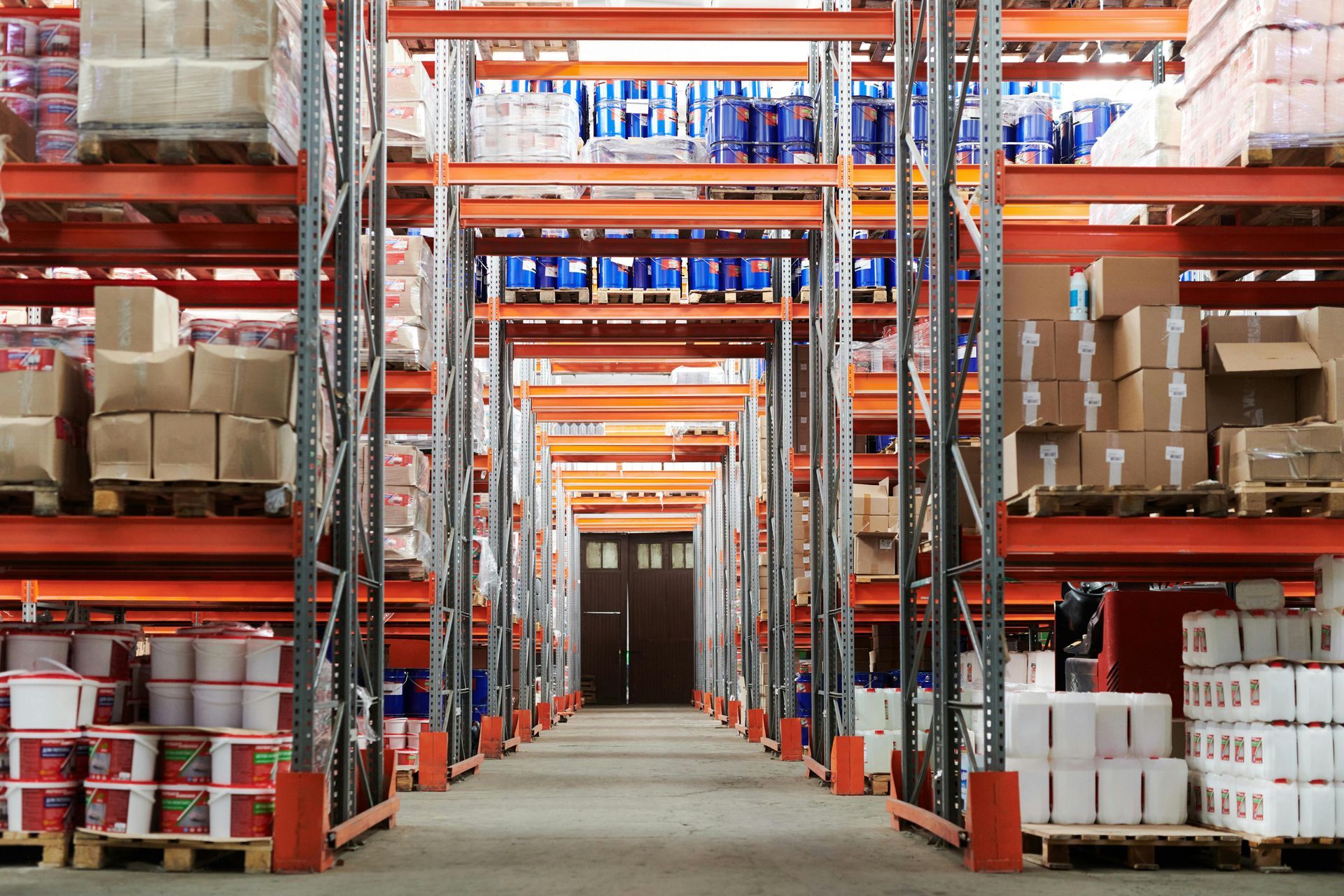